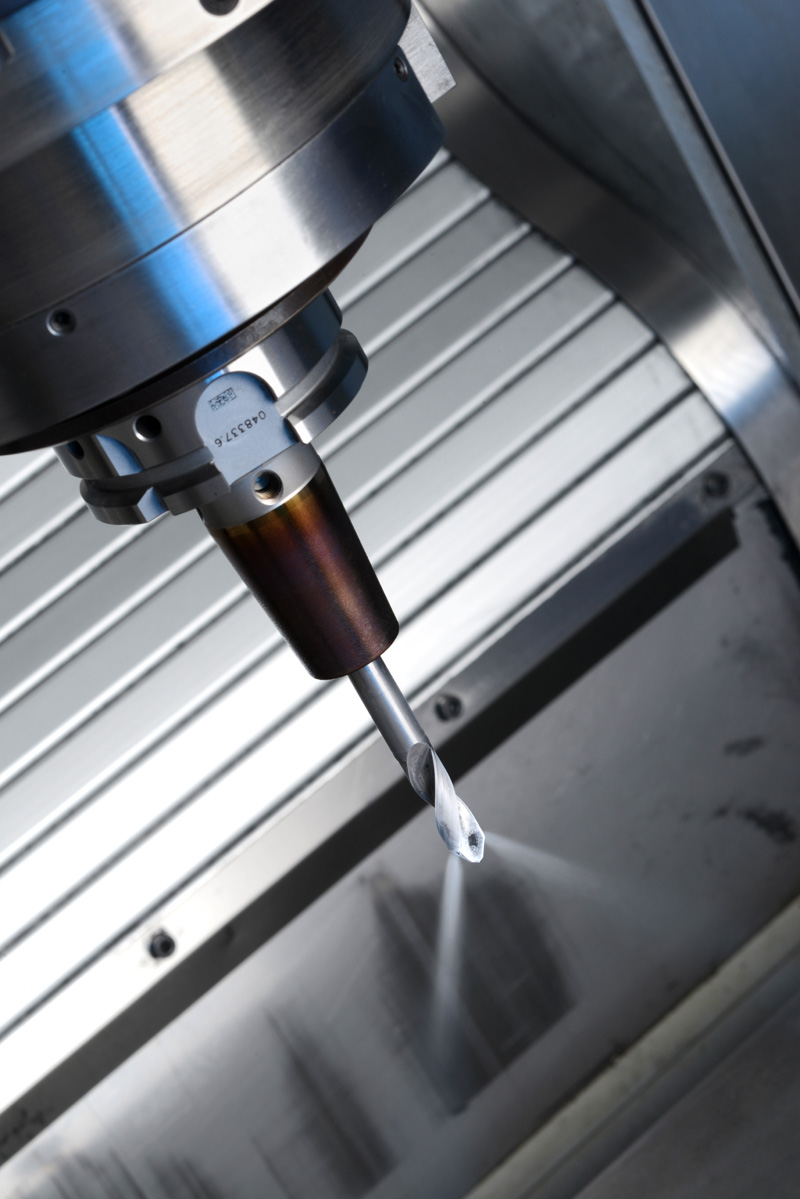
In the following a short summary of reached results for the different technology packages is given:
System Development and Integration
- Design and manufacturing of a custom-made machine spindle with a standard HSK-A63 tool interface, a two-channel cooling-lubrication system and a contact-free energy transmission unit suitable for ultrasonic technology
- Design and manufacturing of tool holder, which converts generator energy into mechanical high-frequency vibration of the drilling tool. A vibration frequency of 32.5 kHz and amplitudes (peak to peak) in the range of 6 to 8 µm were reached using the newly-developed PCD tools
- Since both systems (machine spindle and tool holder) have standard interfaces, they can be easily integrated into any existing or new cutting machine
- Development of new cutting oil compositions for drilling of CFRP and CFRP-Al stacks under cryogenic cooling conditions using ester and saturated fatty alcohols as basic components
Cutting Tool Development
- PCD with average grain size of 10 µm with double-tipped drill for CFRP and single tipped drill with chamfered tool corner for CFRP-Al stacks performed best
- Development and manufacturing of cutting tools with two spiral holes for aerosol supply and one central bore hole with two exits (y-shape) for the supply of liquid CO2
- Offset of higher rod price by more efficient tool manufacturing process
Process Development
- The application of ultrasonic assistance has a clearly measurable effect on the resulting thrust force. With increasing ultrasonic frequency and amplitude, the reduction is more pronounced both for individual CFRP and for stacks. Furthermore, the ultrasonic effect is intensified as tool wear progresses, opening up possibilities for a longer tool life
- Applying ultrasonic vibration with improved tool geometry for CFRP drilling, was found to be an effective way to prevent premature tool damage as observed for dry drilling under specific conditions
- The additional application of two-channel MQL (Minimum Quantity Lubrication)-CO2 technology reduced tool wear significantly, due mainly to the change in fibre cutting behaviour, the use of more efficient coolant-lubrication and improved accessibility for the cooling lubrication media, all of which are related to the interrupted cutting process resulting from ultrasonic assistance.
- One-shot drilling (drilling different workpiece materials with one single tool and process) of FRP-metal stacks is always associated with deviations between the bore hole diameters generated in FRP and the metal part. These deviations are attributable to the different machining behaviours and the related material resilience. When the entire “VibroCool”-technology is applied, these deviations can be reduced by 70% in comparison with a conventional drilling process using standard cooling and lubrication solution.